Industrial sulfur produced by gas recovery in petroleum refineries is an important raw material for chemical, pharmaceutical, rubber, paper, food and other industries . As the arsenic content restricts the quality grade and use of sulfur, it has become an important item for routine detection in industrial sulfur. High-quality industrial sulfur requires that the arsenic content be less than or equal to 0.0001% . The traditional method usually uses microwave digestion atomic fluorescence spectrometry to measure arsenic in industrial sulfur. Low-level arsenic is easily not detected, which cannot meet the quality control requirements for high-quality sulfur in production. Therefore, it is necessary to establish a sensitive and reliable method for the determination of low levels of arsenic in industrial sulfur. This application center uses microwave to digest sulfur, and ICPMS method to determine the content of arsenic in the digestion solution . The method has short analysis time, less reagent consumption, simple operation, good sensitivity and accuracy, and the relative deviation of parallel determination results is ≤4.9%, which is far less than ≤30% specified in the standard. It can be used as an analysis method for arsenic content in industrial sulfur.
Key words: super microwave, ICP-MS, chemical industry, sulfur, arsenic
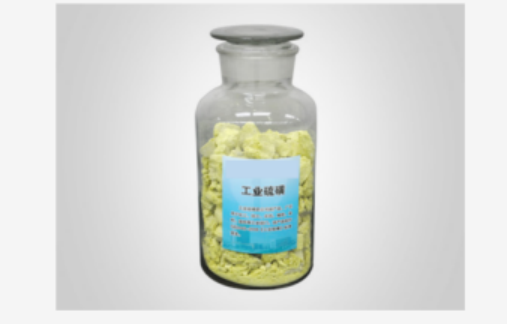
Experimental part
Instrument
Table 1 Inductively coupled plasma mass spectrometer and super microwave digestion instrument

Table 2 Detection parameters of ICP-MS

Reagents and Standards
Reagent: premium pure nitric acid;
Pure water: 18.2 MΩ·cm deionized water (25°C);
Standard solution: single element standard solution of arsenic and germanium, 1000 μg/mL, (National Institute of Nonferrous Metals).
Sample pretreatment
*Determine the weighing amount according to the content of the element to be measured in the sulfur sample, and select the digestion tube of different specifications.
(1) 0.2 g sample pretreatment method
Take 0.200 g of sulfur sample in a 15 mL quartz digestion tube, add 3 mL of nitric acid, shake it up by hand, put it into a digestion tube rack, and transfer it to a super microwave platform. Digest according to the procedure in Table 3, after cooling, dilute to 50 mL with deionized water.
(2) 1 g sample pretreatment method
Take 1.000 g of sulfur sample in a 35 mL quartz digestion tube, add 3 mL of deionized water and 8 mL of nitric acid, shake it up manually, put it into a digestion tube rack, and transfer it to a super microwave platform. Digest according to the procedure in Table 3, after cooling, dilute to 50 mL with deionized water.
Table 3 Super microwave digestion program

0.2 g sample digestion curve
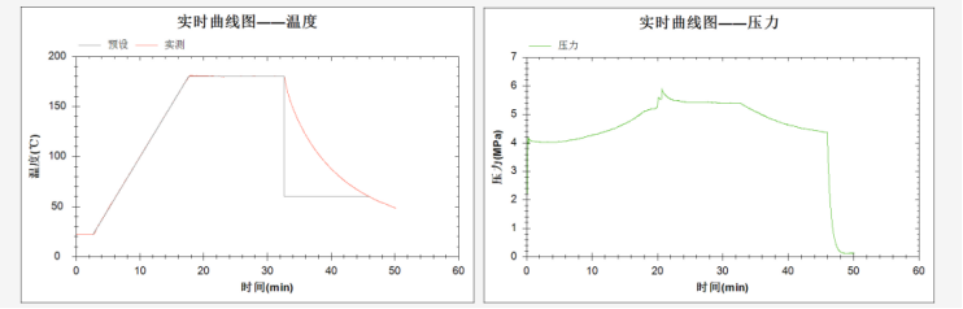
Figure 1 Super microwave heating curve (0.2 g)
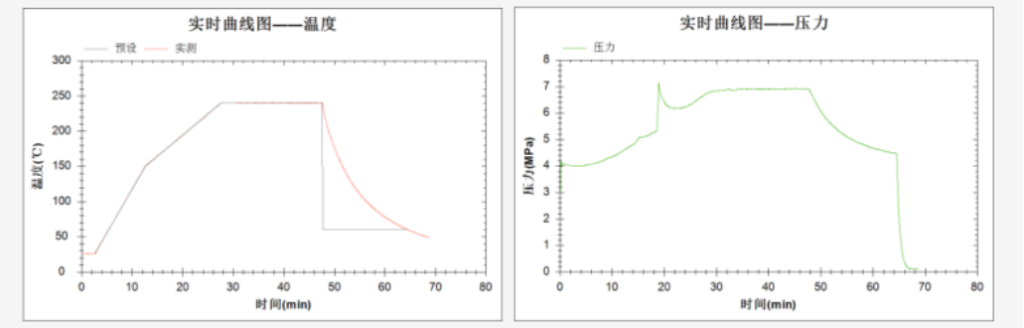
Figure 2 Super microwave heating curve (1 g)
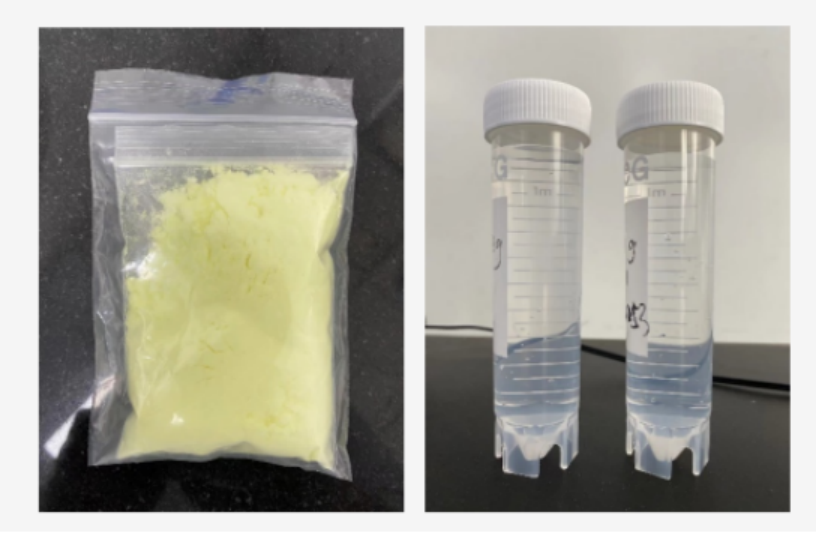
Fig.3 Pictures of sulfur samples before and after digestion
Precision Test
Table 3 Precision test results
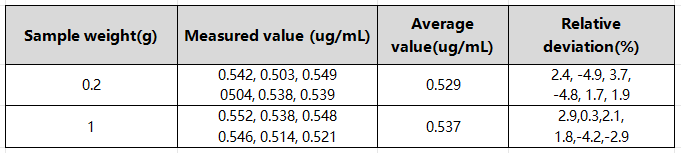
It can be seen from Table 3 that the relative deviation of the parallel determination results is ≤4.9%.
Spike recovery test
Table 4 Test results of recovery rate of standard addition

Epilogue
This method uses super microwave digestion and inductively coupled plasma mass spectrometry to determine the arsenic content in industrial sulfur. The method is easy to operate and has a short operating time. The 0.2 g and 1 g samples are digested, and the recovery rate of the determination is between 93.8-98.9%. The relative standard deviation of the method is less than 4.9%, which can be used as an analysis method for arsenic content in industrial sulfur.
Appendix
Equipment and Consumables Solutions
1. Super microwave configuration details
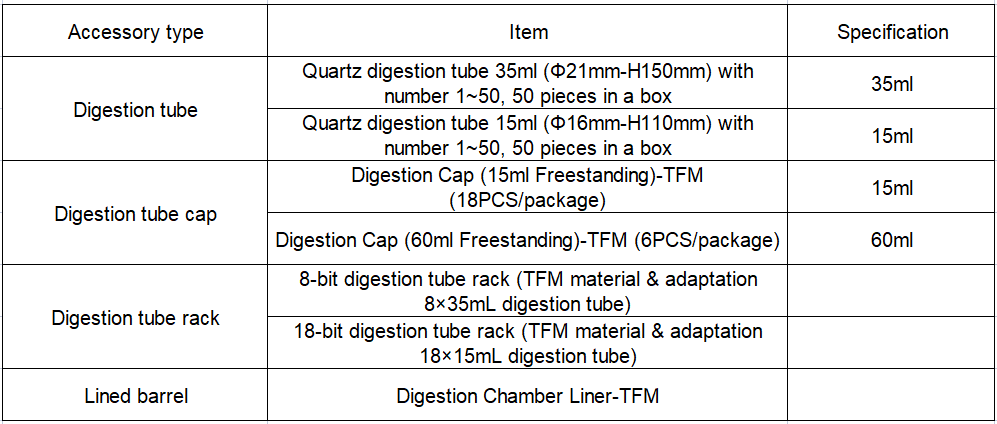
2. Configuration details of SUPEC 7000 standard sampling system
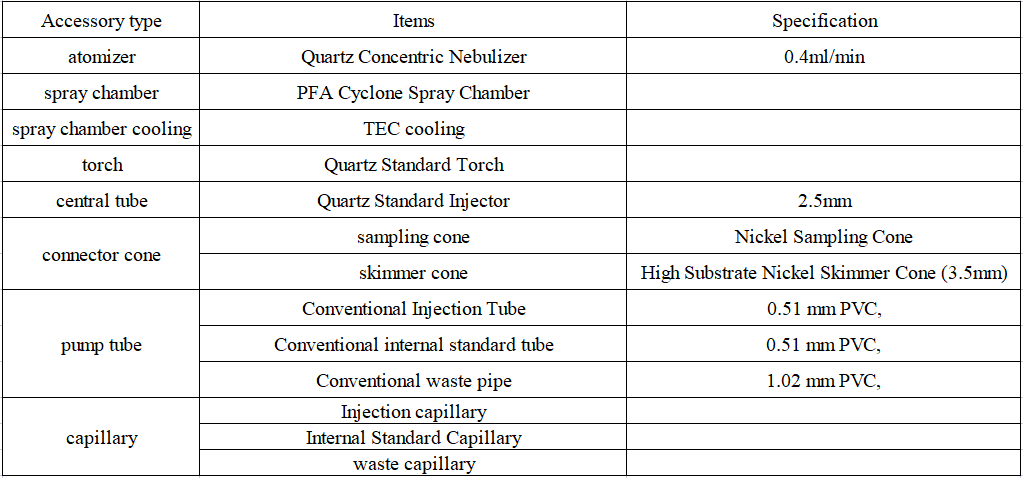
3. Standard products
